How Can Automation Address Manufacturers’ Biggest Invoice Processing Challenges? 26 Feb 2024
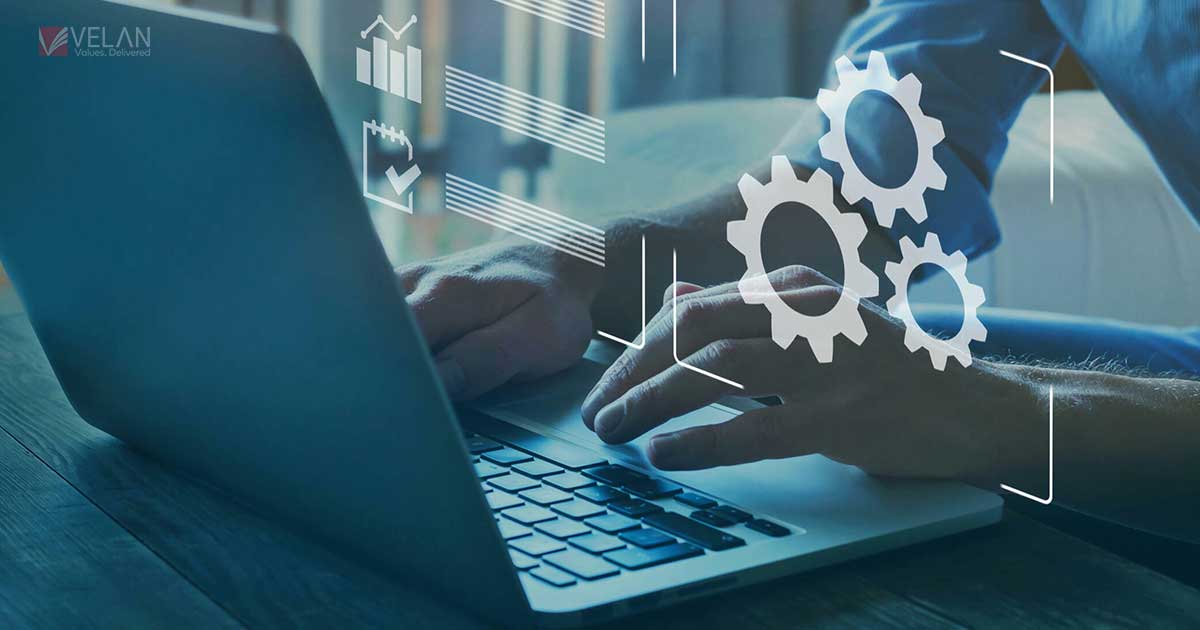
The reputation of your company and relationships with suppliers and distributors may be at risk due to improper invoice processing. A major problem for manufacturers is manually reviewing and processing thousands of invoices without delay or mistakes. Additionally, production and supply delays as well as an increase in processing expenses per invoice, can result from the protracted approval processes required to process invoices by concerned department heads.
Only 24% of businesses that manually handle their invoices (fewer than 20,000 per year) can pay purchase order-based invoices promptly, according to a report from the Institute of Finance and Management (IOFM). The typical cost per invoice for these businesses is $15.97, compared to $12.98 for businesses that use automated invoice processing software.
The manual process’ numerous obstacles for the AP (accounts payment) department in processing invoices have an impact on manufacturing efficiencies. The main issues with processing invoices are discussed in this essay, along with potential technological and automated solutions.
9 Typical manual invoice processing problems that affect manufacturing activities
Processing many invoices manually can be time-consuming and result in payment errors as well as production and workflow inefficiencies. Additionally, it might pose legal and security issues for customers and suppliers.
Processing manual invoices at hidden costs
- The average time taken by organisations to manually process an invoice is 8.3 Days
- Average loss the company has to bear due to duplicate invoices: $12,000
- Average per day hours spent in manual invoice processing: 1 hour 45 minutes, out of 8 hours
The following are some typical issues with manual invoice processing that must be resolved as soon as possible:
Late payments on invoices might cause production and shipments to be delayed:
Manually processing hundreds of invoices may result in errors or delays. For a manufacturing facility to obtain raw materials, machinery, and other equipment, payments to suppliers must be completed promptly. You won’t receive goods on time if invoices aren’t issued or processed on time, which will eventually have an impact on the entire production and supply chain.
Invoice discrepancies might result in late payments and penalties:
Manual processing inevitably results in human mistakes and inaccuracies. Both the sender and the recipient must have full knowledge of the invoice amount, payment method, quantities, rates, billing cycle, etc. when creating or processing invoices.
Any of these can cause a payment delay because the AP department will need more time to verify the information and fix any mistakes. Your accounting departments and suppliers may become confused as a result, which may impact the overall operation. The worst-case situation may require you to pay fines because of late payments.
Insufficient payment of invoices harms relationships with suppliers:
Along with human oversights and inaccuracies, protracted approval processes also slow down the processing and payment of invoices. When processing invoices manually, the procedure and shipment of goods are delayed as the invoices are sent back and forth for approvals between various departments.
Regularly delayed payments can irritate distributors and vendors and affect their cash flow. Long-term effects include those on your company’s reputation, conditions of payment, and supplier relationships.
Manually verifying numerous data points across invoices may result in errors:
If your manufacturing operation has a sizable vendor network, they produce thousands of invoices each year. While some are straightforward to handle, others might be complicated and require multi-step validation of various data points. Any crucial piece of information that is overlooked might lead to misunderstandings among stakeholders and delay the production process.
Incorrect or missing items are another frequent problem when manually verifying data points across numerous invoices. There are times when the vendor’s list of items on the purchase order doesn’t match what you received.
With manual methods, it may take some time to detect that some components are inaccurate or missing from the supplier’s invoice, which could result in a financial loss or production delay.
Missing or duplicate invoices harm the credibility and financial flow
Paper invoices are commonly lost or misplaced during manual approval transfers between departments. Suppliers may send you invoices multiple times if they anticipate a delay in payment or if they are confused.
The AP department and vendors may experience conflict as a result of underpaid or duplicate payments, which will make the recovery process more difficult. Your financial cash flow and supplier relationship will be negatively impacted in either circumstance.
As more time and resources are used, the cost of each invoice rises:
In every business, time is money. You will eventually pay a high price for spending a lot of time and resources on manual invoicing for thousands of invoices annually. The manual method has higher processing costs than the automated method, which can vary for different vendors based on the calculation variables.
The average cost per invoice for manual processing can range from $13 to $40 due to excessive spending on paper, expensive labor, and other resources.
Lack of transparency and management of the production budget and workflow:
The AP department doesn’t have a lot of control or visibility over the spending insights when invoice processing is handled manually. The data is disorganized and congested, with limited visibility for future references, because they employ paper and email systems to obtain approvals and manage bills.
Security and legal issues may arise from failure to comply with financial agreements:
When processing numerous bills manually, vital information might be readily compromised, creating security and legal problems. Data must be stored using the most recent AES encryption to ensure that only authorized users may access it to avoid fraud or loss of essential information.
Insufficient scalability with few resources:
Your needs for processing invoices develop along with your supplier and customer bases. Keeping all of your resources dedicated to manually processing the invoices in this situation leaves little to no space for scalability.
When using a manual procedure, you have to hire and train additional staff, which takes more time and money and is not as effective for processing large amounts of invoices. You will thus waste time on other significant operational and administrative chores.